At present, one of the most significant challenges in LED lighting technology lies in managing heat dissipation effectively. Both LED heat generation and the use of electrolytic capacitors contribute to the short-term limitations of LED lighting fixtures, often leading to premature aging of the light sources. To address this issue, it’s crucial to expel heat as quickly as possible, thereby reducing the internal temperature within the LED lamp. This helps ensure that the power supply operates in a cooler environment, preventing the LED light source from deteriorating prematurely due to prolonged exposure to high temperatures.
Since LED light sources do not emit infrared or ultraviolet rays, they lack any natural mechanisms for heat dissipation. As a result, the primary method for dissipating heat in LED lighting fixtures relies on heat sinks that are tightly coupled with the LED chips. An effective heat sink must possess three key capabilities: thermal conduction, thermal convection, and thermal radiation.
For any heat sink, the ability to rapidly transfer heat from the heat source to its surface is fundamental. However, the critical aspect is how well it can dissipate this heat into the surrounding air, primarily through convection and radiation. While thermal conduction serves to establish the pathway for heat flow, thermal convection plays the dominant role in the actual heat dissipation process. The efficiency of a heat sink depends largely on factors such as its surface area, geometric shape, and the intensity of natural convection. Radiation serves as a supplementary mechanism. Typically, if the distance between the heat source and the heat sink's surface is less than 5mm, materials with a thermal conductivity greater than 5 will suffice for transferring the heat, while the rest of the heat must be dissipated via convection.
Most LED lighting still employs low-voltage (VF=3.2V), high-current (IF=200-700mA) LED chips. Given their high operational heat output, aluminum alloys with excellent thermal conductivity are typically used. These include die-cast aluminum heat sinks, extruded aluminum heat sinks, and stamped aluminum heat sinks. Die-cast aluminum heat sinks involve a pressure casting technique where molten zinc-copper-aluminum alloy is poured into a die-casting machine and shaped according to a pre-designed mold.
Below is a comparative analysis of the five types of heat sinks:
**Die-Cast Aluminum Heat Sink**
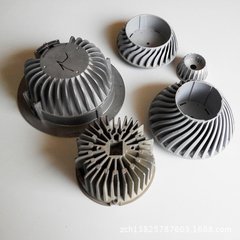
Die-cast aluminum heat sinks are cost-effective to produce, but their heat dissipation fins cannot be made very thin, limiting the overall heat dissipation area. Common materials used include ADC10 and ADC12.
**Extruded Aluminum Heat Sink**
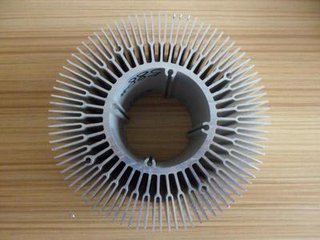
Liquid aluminum is extruded through a fixed mold and then machined into the desired heat sink shape. This process is more expensive, but the extruded fins can be made much thinner, maximizing the heat dissipation area. When these fins operate, they naturally form an airflow that enhances heat dissipation. Common materials are AL6061 and AL6063.
**Stamped Aluminum Heat Sink**
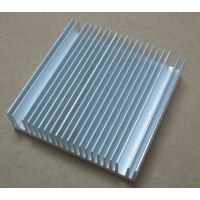
Stamping involves using punching machines and molds to create cup-shaped heat sinks from steel or aluminum alloy plates. The surfaces of these heat sinks are smooth, but their heat dissipation area is limited due to the absence of fins. Common materials include 5052, 6061, and 6063 aluminum alloys. These heat sinks are lightweight and cost-effective.
Aluminum alloy heat sinks offer excellent thermal conductivity and are well-suited for isolated switching constant current power supplies. For non-isolated switching constant current power supplies, the design must incorporate structural features to separate AC and DC, high and low voltages, to meet certifications like CE or UL.
Hongkong Onice Limited , https://www.ousibangvape.com