At present, one of the major challenges in LED lighting technology is dealing with the issue of heat dissipation. Heat generated by LED lights and electrolytic capacitors can lead to premature aging of the light source and hinder the long-term development of LED lighting solutions. To address this, it's crucial to efficiently dissipate heat from the LED lamp as quickly as possible, thereby reducing the internal cavity temperature and preventing the power supply from operating in excessively high temperatures. This is essential to avoid the early degradation of the LED light source due to prolonged exposure to heat.
Unlike traditional light sources, LED lamps do not emit infrared or ultraviolet rays, meaning they lack any inherent radiation-based heat dissipation capabilities. As such, the heat dissipation mechanism of LED lighting relies entirely on the heat sink, which is tightly coupled with the LED chip. A good heat sink must possess excellent thermal conductivity, convective properties, and radiative abilities.
When it comes to thermal management, the key role of a heat sink is not just to transfer heat away from the source but also to disperse it effectively into the surrounding air. While thermal conduction plays a part in moving heat along its path, thermal convection is the primary method through which heat sinks dissipate energy. The overall effectiveness of a heat sink depends significantly on its surface area, shape, and the intensity of natural convection currents. Typically, if the distance between the heat source and the heat sink’s surface is less than 5mm, materials with thermal conductivity greater than 5 can handle the initial heat transfer. Beyond that, the bulk of the heat dissipation is handled by convection.
Most LED lighting systems still utilize low-voltage (VF=3.2V), high-current (IF=200-700mA) LED chips. These generate significant heat during operation, necessitating the use of materials like aluminum alloys with high thermal conductivity. Commonly used heat sinks include die-cast aluminum, extruded aluminum, and stamped aluminum varieties.
Let’s take a closer look at these three types of heat sinks:
**Die-Cast Aluminum Heat Sink**
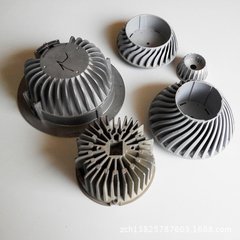
Die-cast aluminum heat sinks are produced by injecting molten zinc-copper-aluminum alloy into a die-casting machine and then casting it into a pre-designed mold. This process results in cost-effective production, but the heat dissipation fins tend to be thicker and harder to refine, limiting the overall heat dissipation area. Common materials used include ADC10 and ADC12.
**Extruded Aluminum Heat Sink**
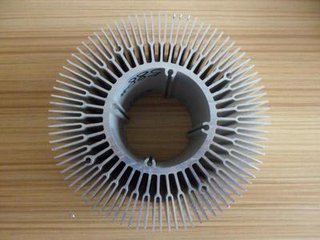
In this method, liquid aluminum is pushed through a fixed mold to form a bar, which is then machined into the desired heat sink shape. The extrusion process allows for thinner fins, maximizing the heat dissipation area. Airflow naturally enhances heat dissipation when the fins are in use, making this type of heat sink highly efficient. Common materials include AL6061 and AL6063.
**Stamped Aluminum Heat Sink**
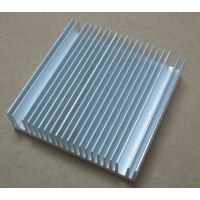
Stamped aluminum heat sinks are created by punching and pulling steel or aluminum alloy sheets using presses and molds, resulting in cup-shaped designs. These heat sinks feature smooth inner and outer peripheries but lack fins, thus limiting their heat dissipation area. Materials typically used include 5052, 6061, and 6063 aluminum alloys. Stamping offers lightweight solutions with high material efficiency, making it a cost-effective option.
Aluminum alloy heat sinks generally provide excellent thermal conductivity and are well-suited for isolated switching constant current power supplies. However, for non-isolated switching constant current power supplies, additional structural design considerations are needed to separate AC and DC, high voltage and low voltage components, ensuring compliance with standards like CE or UL.
Efficient heat dissipation remains a critical factor in extending the lifespan of LED lighting systems, and ongoing advancements in heat sink technology will continue to play a vital role in overcoming these challenges.
Hongkong Onice Limited , https://www.ousibangvape.com